I was watching some old clips of an Anthony Bourdain series called “Raw Craft” this afternoon. There is a quote in the intro that made me smile and nod.
“The term “hand-crafted” gets thrown around a lot these days. It’s become a movement, a “trend”, and it can obscure the passionate people who actually make things by hand.”
That term does get thrown around a lot.
Add “hand made” to the tagline of any product and the price jumps dramatically, and so does the mystery. When I hear that phrase, I automatically wonder: Who's hands? Are those hands being exploited? Are those hands being taken care of properly? Why are those hands special? How long have those hands been making? Depending on the product or situation sometimes the answers are quickly evident. Sometimes they are hidden behind layers of false romance and branding that are hard to peel back to see what we're really buying into.
Ultimately we can't always know, and that's ok. I don't want to throw stones at anyone else's business efforts. I cannot control what other people do, or the standards they set, but I can take this opportunity to tell people who are considering becoming a patron or friend of our project, exactly what I mean when I use the words "hand made".
There are three points that I feel the need to communicate.
The first thing I'd like to be loudly explicit about are our processes. I take immense pride in making garments that are long, hard wearing friends you will be able to hold onto for decades.
On "Hand made" Tailoring:
I am deeply in love with analogue hand-craft. Like most tailors, I do a large amount of hand sewing, hand embroidery and hand buttonholing. I like it that way, and I never want to change. In a world full of machinists, I find it is a political act to slow down and use your hands. However, I tend toward the English when it comes to sensibility and stability. It is necessary, for the sake of making a durable garment, to machine over some seams that may receive a good deal of stress, or the seams that machines do better.
For example: It is practical and sensible to use a machine when sewing the long seams on a pair of trousers. The stitching is even, it’s sturdy, and I also always machine twice, for extra strength. These seams receive stress when we bend our knees, crouch, or even just sit in a chair. I’d like the trousers we produce to last as long as possible, so we use a sewing machine from time to time. I run and guide the machine with my hands, but in that case I think those seams are “machine sewn”. That being said, all of the bar tacks, pick stitching, hemming, embroidery, pad stitching, and felling is done 100% by hand.

On Hand Made Knitwear:
I have never, and will never use a knitting machine. Every knitted item, every hat, jumper pair of mittens, or scarf that comes through the store will have been on a pair of bamboo needles in my studio at one point. Those needles are usually varying from 2.00mm to 4.00mm. I form every stitch in each of my garments and constantly check for even tension and correct measurements. I tend to only sell “high gauge” knitted pieces because while they take a lot longer to make, they last much longer than low gauge hobbyist work.
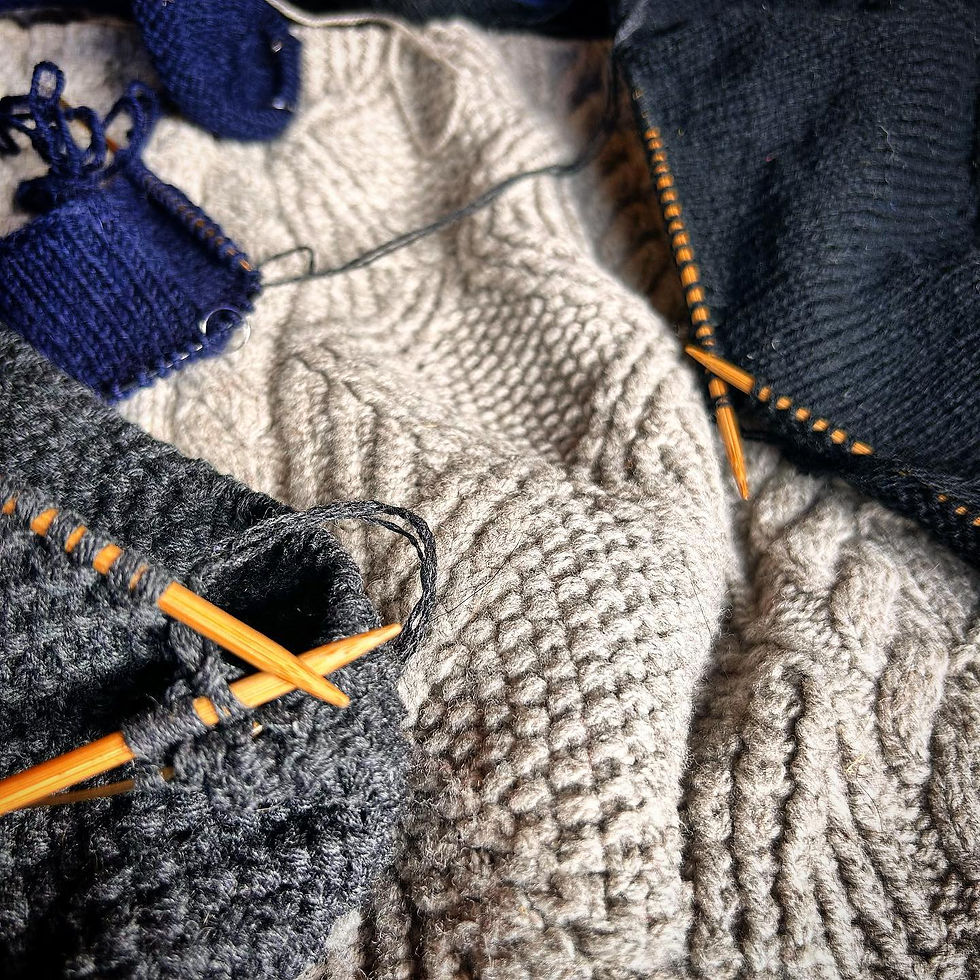
The next thing that concerns me most of the time when thinking about "Hand made" is who's hands are doing the making?
in 2017 I closed my brick and mortar yarn store, and while it was a relief in some ways, there were a few people I desperately missed. Two of the most talented knitters that frequented my store have returned to my new atelier to help me do cottage industry style production for a lovely menswear brand called "Brycelands & Co.", and to build a collaborative atmosphere where we can enjoy each other's creativity, keep each other company from time to time, and make beautiful things. Every item in my little marketplace has been produced within these four walls, designed by us, and finished by me. These two women are paid exactly the same amount for their work that I am. We sometimes all three work together on one garment, but also create things separately. If you would like to know which of us knitted the garment you choose, please just ask. I am the kind of an "all rounder" sweater maker, Yukie often focuses on Irish cables, and Hisako loves making whimsical children's clothing and toys. We each have a niche, but work wonderfully together.
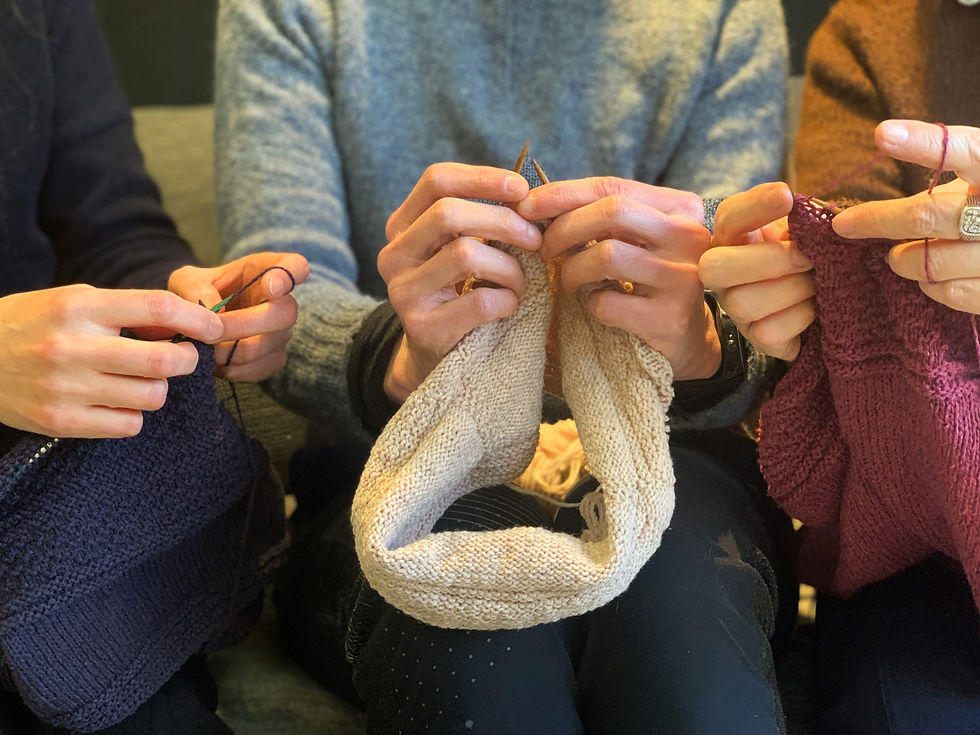
Pricing is personal, but I believe in transparency and helping people understand why something one might feel is “expensive” is worth so much. The price of our hand work basically boils down to two things: materials and time.
On Materials:
I use only rare sheep breed yarns and cloth, and small batch hand knitting yarns in my pieces (unless otherwise requested). These are the best and most storied wools from all over the world, and mostly come from producers I have friendships or long working relationships with. They are materials I truly believe in, and wear regularly myself. I will happily include information and original labels from the yarn used. I also do the best I can to use wool producers who raise sheep for wool only, but this is a difficult request to meet 100% of the time. Most of these materials cost from $30-90 (USD) per 100g. Many of these wool companies survive on love, as the world has moved away from natural fibres. I am always pleased to be able to support these small makers, and collaborate every time I receive the chance. It typically requires about 5-600g of hand knitting yarn to produce one jumper, so materials alone often cost up to 30% of the final price of the finished garment.
Time: All of the garments on the website are designs from our atelier. Designing an item can take between 5-15 hours. I knit, wash, finish and press everything manually. A sweater usually takes about 130-150 hours to knit. A hat requires between 3-10 hours. Gloves, scarves, etc. come somewhere in between. Gauge, and size play a large role in pricing a finished piece.
What you receive:
Each of our pieces comes finished and pressed in an okayama denim furoshiki. If it is a jumper or large item we box this before we send it.
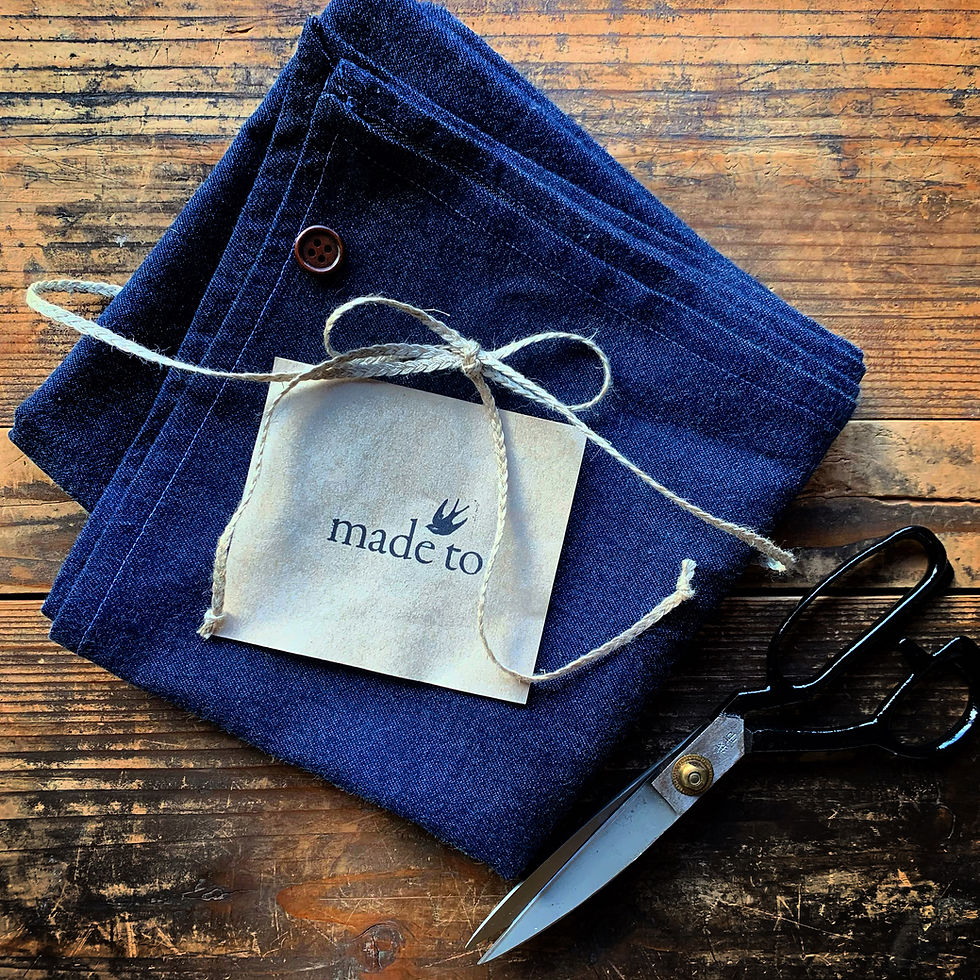
Each of our pieces come with a lifetime mending policy. All of the things I've made in my life are like friends. I am so happy when I get to see them again, and even more if they have been used and worn. If our customers end up with a hole, or a place that needs to be mended, I will do that for free for the lifetime of the garment. The duration of that life is decided ultimately by the person who purchased the item. We of course do not cover shipping fees from abroad for mending (unless specified and agreed upon according to the TOS), but the actual labor of mending is covered by us, with pleasure.
Thank you for taking the time to let me be clear, so I can feel a bit safe in the knowledge that I told my truth, and everyone understands clearly that the little piece of myself that I'm selling here is an honest attempt to put quality and a personal touch back out into the world.
We were made to be honest about what we do.
If you'd like to visit the atelier, or know more about our work, please use the contact form to ask questions or make an appointment.
Comments